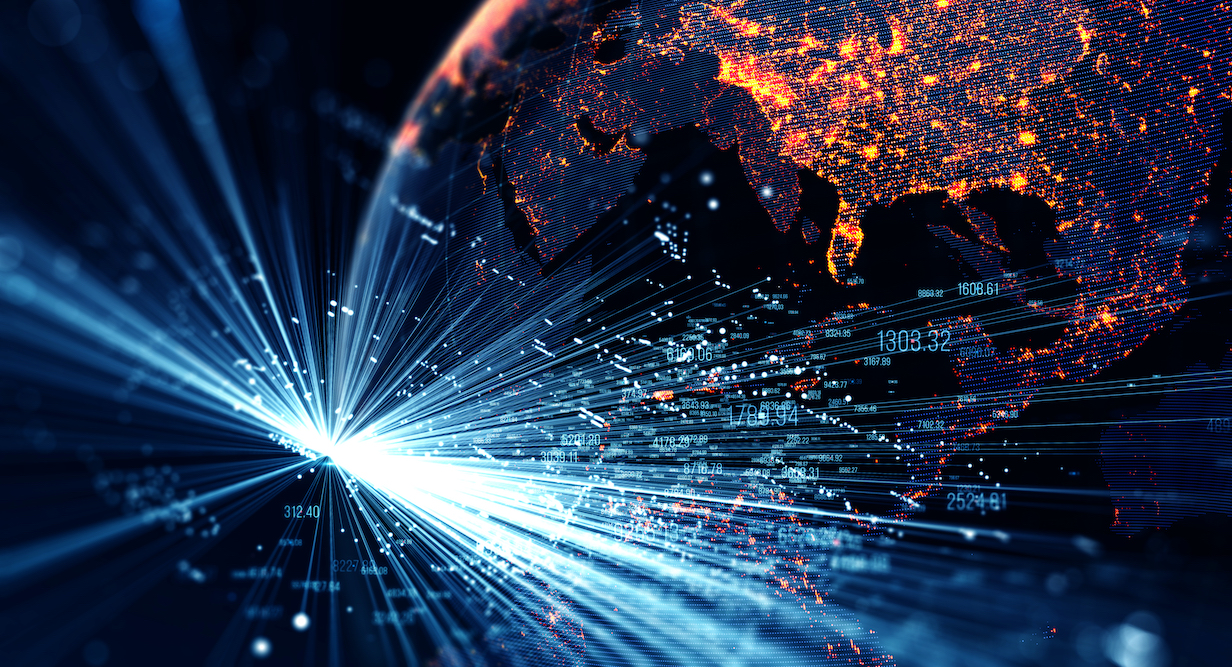
Articolo di Massimo Gozzi
Sempre più frequentemente ci imbattiamo nel termine “Digital Energy”, termine che sta ad indicare la possibilità di utilizzare le tecnologie digitali per “controllare” i consumi di energia, in particolare di un insediamento industriale. Ma dietro questo termine si nasconde molto di più: l’uso di tecnologie digitali sempre più avanzate è ben profondo ed interessa l’intera filiera dell’energia, ovvero dalla produzione al consumo finale per passare attraverso la distribuzione, interessandone quindi tutte le fasi. L’impiego potenziale del digitale va quindi ben oltre il solo controllo.
Parlare di Digital Energy significa parlare di architetture complesse, che infatti – moltre ai sistemi hardware e software per il monitoraggio e l’azionamento dei diversi impianti energetici – comprendono i sistemi di trasmissione dei dati e la loro elaborazione. Significa parlare di architetture distribuite ed aperte, con funzioni di elaborazione dei dati che dall’essere “a bordo macchina” diventano sempre più nel “cloud”, elaborate con gli strumenti di “(big) data analytics”.
In buona sostanza parlare di Digital Energy significa parlare di un’architettura che è composta da 5 diverse e concatenate macro voci:
- Apparati fisici: sono tutti gli apparati che consentono di raccogliere dati in merito alle condizioni di funzionamento di un dato asset, consentendo la valutazione sia di variabili interne che di fattori esogeni. In tale famiglia rientrano tipicamente contatori, sensori e attuatori.
- Trasmissione e comunicazione: tecnologie che consentono la trasmissione dei dati fino alla piattaforma di immagazzinamento e la comunicazione tra i vari dispositivi digitali.
- Immagazzinamento e trasmissione del dato: tecnologie per lo stoccaggio delle informazioni che devono essere implementate per la trasmissione del dato all’esterno per le funzionalità di Data Analytics.
- Funzionalità del dato: tecnologie che, a valle della raccolta e dell’immagazzinamento dei dati permettono di ottenere “visibilità” sul funzionamento del macchinario, consentendo azioni di controllo e programmazione per l’ottimizzazione delle performance.
- Valorizzazione del dato: tecnologie che possono ulteriormente valorizzare i dati raccolti, grazie ad esempio a strumenti di Big Data Analytics.
Le capacità dei prodotti interconnessi spaziano dal più semplice monitoraggio delle condizioni di funzionamento di un impianto, con la conseguente segnalazione di eventuali anomalie, al controllo, all’ottimizzazione, fino allo sviluppo di una certa autonomia del prodotto. Software evoluti infatti consentono di decifrare in modo sempre più accurato le informazioni contenute nei Big Data, creando per di più nuove opportunità di business, legate alla condivisione dei dati stessi ma anche a quella dei risultati delle elaborazioni numeriche.
Le soluzioni Digital Energy per lo Smart Manufacturing
Tra i differenti ambiti in cui possiamo spaziare all’interno della filiera energia, possiamo concentrarci su quello dell’utilizzo industriale, ed in particolare dell’industria della produzione, in quanto di diretto interesse per gli operatori del settore in qualità di consumatori di energia.
In ambito industriale, sia nelle grandi imprese che nelle PMI, stiamo assistendo ad una digitalizzazione sempre più accelerata. Le nuove tecnologie consentono di avere accesso a dati e informazioni che tuttavia necessitano di essere interpretati con un linguaggio comune, trasformando il dato in sé in opportunità di sviluppo e di business.
Sostenibilità economica: benefici delle soluzioni Digital
Vediamo dapprima come, in linea generale e per ogni comparto manifatturiero, possano essere valutati e identificati i benefici economici delle soluzioni Digital, applicate ai consumi energetici, nell’elenco seguente:
- Miglioramento dell’efficienza energetica: i processi possono essere ottimizzati in termini di efficienza energetica grazie al monitoraggio delle condizioni di funzionamento. La consapevolezza del dato energetico abilita interventi di carattere gestionale ma anche tecnologico con l’introduzione di nuove soluzioni.
- Aumento della produttività: i processi industriali possono essere ottimizzati dal punto di vista dell’utilizzo di materia prima, velocità di produzione e qualità del prodotto, grazie al monitoraggio dei parametri di funzionamento e all’integrazione delle informazioni su vari livelli del processo produttivo.
- Miglioramento del time-to-market: l’ottimizzazione e il miglioramento delle attività produttive consente di raggiungere il mercato in tempi più brevi. La digitalizzazione costituisce quindi un vero e proprio differenziale competitivo.
- Gestione ottimizzata degli asset: il monitoraggio delle condizioni di funzionamento consente di intervenire con azioni manutentive mirate e di carattere preventivo. Ciò permette di limitare i tempi di fermo macchina e di aumentare la vita utile dei macchinari.
Per ridurre la complessità di rappresentazione, i 4 possibili benefici dell’adozione di soluzioni Digital sono stati ricondotti a due macro-variabili, definite come il miglioramento dell’efficienza energetica (che incorpora solamente il primo dei benefici elencati) e l’aumento della redditività dell’impresa (dove sono inclusi gli effetti relativi all’aumento della produttività, al miglioramento del time-to-market e alla gestione ottimizzata degli asset).
Tali benefici variano a seconda dell’architettura Digitale considerata e denotano chiaramente un’entità maggiore nel caso dell’installazione di un’architettura più evoluta e complessa.
Nel caso in cui l’intervento richieda anche l’installazione di un sistema di monitoraggio, si ha generalmente un incremento di circa 10 punti percentuali alla voce di risparmio energetico, anche se questa ovviamente si accompagna ad una accresciuta necessità di investimento.
Venendo alla quantificazione dei benefici, come si è già detto, e come confermato dalla rilevazione empirica e dai casi studiati, la valutazione dei benefici – fatta in percentuale – può essere invece considerata sufficientemente “stabile” tra i diversi settori merceologici analizzati.
E’ evidente che ogni impresa, per dimensione, complessità e articolazione del processo produttivo, rappresenta un “unicum”, che pur tuttavia appare possibile ricondurre, almeno in prima approssimazione, all’interno di un range di valori.
Come elemento di valorizzazione dell’aumento della redditività è stato considerato I’EBITDA al netto delle tasse, mentre il risparmio energetico si ripercuote direttamente sulla bolletta energetica dell’operatore industriale.
Le possibili Architetture Digital
L’implementazione di un’infrastruttura digitale può essere organizzata secondo diverse configurazioni tecnologiche.
Per semplicità di trattazione sono state denominate Architettura “Basic”, “Intermediate” e “Advanced” proprio a significare la differenza di complessità. Il livello di complessità delle soluzioni implementabili è chiaramente un “continuum” e le possibili configurazioni tecnologiche sono innumerevoli, ma tali configurazioni rientrano comunque all’interno degli estremi qui identificati e descritti nel dettaglio che segue:
• Basic: la raccolta dati viene effettuata interfacciandosi con i sistemi di controllo e di comunicazione già installati negli impianti di produzione. I software di elaborazione dati si limitano alle funzioni di monitoraggio e di “dashboard”, ovvero raccolta dati di sintesi.
• Intermediate: in aggiunta ai sistemi di controllo già esistenti vengono installati attuatori che sono in grado di agire sull’impianto a seconda delle informazioni raccolte. Il software di elaborazione dati ha quindi un grado di “intelligenza” maggiore in grado di migliorare anche l’automazione industriale.
• Advanced: l’intervento consiste nell’installazione di sensori e attuatori. E’ necessario inoltre installare una infrastruttura di telecomunicazione avanzata che risponda alle nuove esigenze digitali. Strumenti di Advanced Data Analytics e Machine Learning consentono il controllo e l’ottimizzazione in tempo reale della produzione.
Il caso dell’industria
Calandoci ora nella realtà di nostro principale interesse, ovvero dell’industria, i tempi di ritorno (PBT: Pay Back Time) variano dai 3 ai 6 anni. Gli “economics” migliori sono appannaggio dell’architettura denominata “Basic” installata in un’impresa che già presenta un sistema di monitoraggio (PBT di circa 3 anni e IRR: Internal Rate of Return, compreso tra 35 -40%).
La soluzione “Basic”, meno gravosa dal punto di vista dell’investimento, risulta però essere anche la meno fruttuosa in termini di flussi finanziari ad essa associati. Inoltre la differenza di flussi finanziari tra la soluzione con e senza sistema di monitoraggio energetico è dovuta principalmente alla quota di risparmio energetico, dal momento che l’installazione di un sistema di monitoraggio energetico ha un impatto trascurabile sulla produttività.