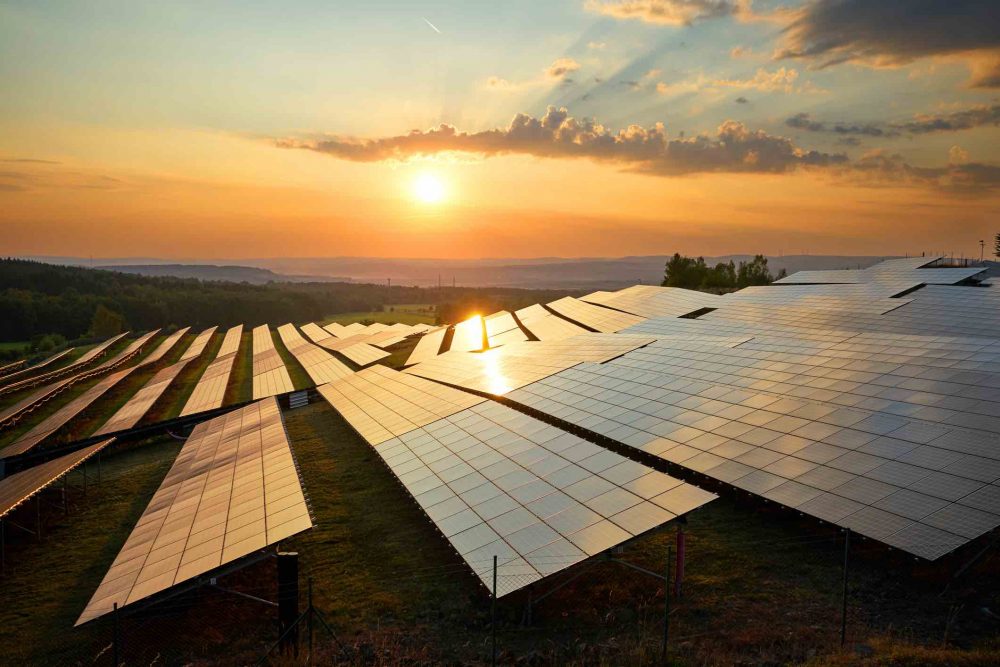
Il problema del risparmio energetico nell’industria tessile
Soprattutto in situazioni difficili di approvvigionamento energetico, l’efficienza degli impianti può essere notevolmente incrementata con tecnologie di risparmio e razionalizzazione dei consumi.
L’efficienza energetica in ambito industriale è un fine da perseguire sempre, a maggior ragione quando l’approvvigionamento di risorse energetiche si fa difficile se non addirittura critico. Per dare concretezza, vediamo il caso di una industria manifatturiera del settore tessile, azienda che si occupa della preparazione, della tintoria, della stampa e del finissaggio dei tessili e degli articoli di vestiario su tessuti in cotone, poliestere, cupro, modal, lana, acrilico, nylon, poliammide, lino e seta.
È importante, per una valutazione degli interventi di efficientamento, esaminare approfonditamente la situazione produttiva aziendale. In questo caso il mix produttivo comprende tessuti e maglie a base di fibre naturali, artificiali, sintetiche e miste. Il lavoro nei reparti di produzione è continuo, suddiviso su tre turni da otto ore ciascuno, per cinque giorni alla settimana. Il volume della produzione e le percentuali di categoria di tessuto prodotto sono funzione delle richieste di mercato e variano, stagionalmente, per assecondare le esigenze commerciali. Per questo motivo il processo produttivo può risultare molto complesso, ed è la ragione per cui si rende necessaria una Diagnosi Energetica (peraltro imposta per legge per determinate categorie di azienda).
Ciclo produttivo e ausiliari di stabilimento
Pertanto il primo passo da eseguire per la redazione di una diagnosi energetica che permetta di caratterizzare e giustificare i consumi energetici è quello di quantificare e analizzare i carichi energetici del ciclo produttivo. Per quanto riguarda infatti i carichi relativi correlati alla produzione, quindi le attività principali, viene generalmente effettuata una suddivisione in base ai reparti, in precedenza dettagliati, più alcuni sotto-reparti di importanza minore dato il loro scarso utilizzo.
Tra i servizi ausiliari (produzione e distribuzione di aria compressa, vapore, acqua calda o surriscaldata), invece, si considerano le aree a servizio dei processi di produzione, tra cui: la centrale frigo, la centrale termica (con un assorbimento elettrico generalmente non indifferente), la sala compressori (compresa degli essiccatori), le stazioni di trattamento e depurazione dell’acqua in ingresso e uscita allo stabilimento e il gruppo elettrogeno di continuità.
A titolo indicativo, i reparti più energivori in termini di consumi elettrici sono la Stampa, il Finissaggio e la Preparazione; insieme questi reparti costituiscono la gran parte dei consumi delle attività produttive. Per quanto riguarda il reparto stampa, sono le stampanti digitali ink-jet ad avere i consumi maggiori; questo è imputabile al fatto che tali macchinari, oltre ad avere un loro computer di bordo atto alla scelta del disegno di stampa, sono anche corredati da diversi motori elettrici che consentono la movimentazione del tessuto e da speciali lampade ad infrarossi che, coadiuvate dall’uso di energia termica, permettono l’asciugatura della stampa sulle fibre.
Sul fronte dei consumi per ausiliari, i reparti di depurazione e trattamento delle acque raggiungono quasi la metà dei consumi, costituiti da sistemi di filtraggio e pompaggio. L’altra quota maggioritaria è da attribuire alla sala compressori d’aria, la quale serve la maggior parte delle macchine produttive. Seguono infine la centrale frigorifera, la centrale termica e un gruppo di continuità.
Passando ai servizi generali, ovvero ai servizi non direttamente coinvolti nella produzione (illuminazione dei capannoni, consumi elettrici e termici degli uffici, mensa ed altro) spesso una buona parte dei consumi è registrato dalle unità di trattamento aria, per la maggior parte a servizio dell’area produzione dello stabilimento e in parte minore per gli uffici. La quota restante rientra nei consumi per l’illuminazione, i quali, possono risultare già limitati in quanto la maggior parte dei punti luce, un tempo con tecnologia obsoleta, sono generalmente già sostituiti con la nuova tecnologia a LED, più performante e con consumi molto ridotti.
Indici di prestazione energetica
Dopo l’analisi critica dei consumi energetici di stabilimento e la relativa loro caratterizzazione in relazione ai dati di produzione (ovvero la loro attribuzione alla funzione produttiva pertinente), il passo successivo è quello della creazione degli indici di performance energetica (EnPI), i quali sono fondamentali per valutare lo stato energetico e prestazionale di un sito produttivo. In sostanza si tratta di attribuire un consumo che è stato destinato ad una unità di prodotto. Nel caso specifico l’unita di prodotto può essere il metro di tessuto prodotto in uscita dallo stabilimento, costituendo in tal caso un indice generale che va riferito sia al consumo di energia elettrica (kWh/m) che al gas naturale (sempre in kWh ma termici).
L’importanza dell’individuazione degli indici energetici risiede anche nella confrontabilità con indici di riferimento presenti in letteratura tecnica o, in alcuni casi, posseduti da associazioni di settore.
Gli interventi conseguenti
Gli interventi individuabili a seguito della Diagnosi Energetica possono essere classificati in due ambiti: Interventi Tecnologici e Interventi Gestionali. I primi sono interventi relativi all’efficienza delle utenze, sia elettriche che termiche e possono includere sia le aree di produzione che i servizi ausiliari e quelli generali ma lo scopo è sempre lo stesso: ridurre i consumi a parità di efficienza del servizio.
L’impianto di generazione dell’aria compressa è di solito una tra le aree più promettenti per attuare interventi di risparmio energetico, poiché la compressione dell’aria è un processo termodinamico con bassa efficienza, per il fatto che il rapporto tra l’aria prodotta e l’energia elettrica consumata dal compressore è relativamente basso. A tal scopo l’installazione di inverter (avviatori a frequenza variabile) su compressori a velocità fissa consente, con il variare della velocità del motore, di adattare al meglio la produzione del compressore alle richieste dell’impianto, consumando meno energia.
Vi sono inoltre interventi che riguardano la produzione di uno o più vettori energetici, come, ad esempio e tipicamente, l’installazione di un impianto fotovoltaico, spesso in aggiunta a un cogeneratore.
Entrambi questi interventi, consistendo in installazioni di generatori di energia (solo elettrica, nel caso dell’impianto fotovoltaico, combinata elettrica-termica con la cogenerazione), contribuiscono a coprire parte dei consumi elettrici di stabilimento, fornendo in questo modo all’azienda una possibilità di approvvigionarsi in misura minore dall’esterno.
Del fotovoltaico si sa già molto, è una opportunità che si sta rendendo sempre più interessante a causa dell’abbattimento del costo dei componenti dell’impianto (pannelli e equipaggiamenti elettrici), ed è particolarmente interessante qualora sussista la possibilità di occupare tetti di capannoni, altrimenti non utilizzati.
Passando alla Cogenerazione, l’interesse su di essa riguarda il processo di produzione energetica, che prevede la generazione di energia elettrica e calore nello stesso impianto, quindi utilizzando la stessa fonte di energia primaria. L’idea di base su cui si fonda questo sistema è quella di voler recuperare parte del calore sviluppato dal ciclo termodinamico, il quale può essere impiegato per sopperire alle eventuali richieste di energia termica all’interno dell’azienda. Questo sistema può incrementare l’efficienza fino ad oltre l’80% (percentuale di sfruttamento dell’energia primaria, ad esempio gas naturale) con un vantaggio notevole sui costi di approvvigionamento del combustibile fossile e una minore emissione di inquinanti, come i gas climalteranti.
Relativamente agli Interventi Gestionali, si tratta di azioni volte a diminuire e razionalizzare i consumi energetici attraverso l’adozione di pratiche, che pur non agendo in modo diretto sui macchinari, ne ottimizzano il funzionamento attraverso un controllo indiretto; questo controllo può avvenire attraverso attività virtuose da parte del personale addetto (spesso codificate in procedure aziendali, ad esempio spegnimento delle utenze a fine turno lavorativo) o attraverso sistemi di misura in telegestione, che permettano il monitoraggio istantaneo dei componenti consentendo quindi l’intervento tempestivo nel caso di consumi anomali.
Altri comparti dell’industria tessile
Quanto detto sino ad ora può essere esteso anche ad altre produzioni nell’ambito dell’industria tessile. La scelta, ad esempio, di installare un sistema di cogenerazione nell’ambito di un’industria tessile che tratta ad esempio di lavaggio e tintura porta notevoli benefici a livello operativo, economico e ambientale, in quanto si tratta di fasi in cui è necessaria una grande quantità di calore. È dunque vantaggioso avere un impianto che riesca a recuperare l’energia termica dei macchinari durante le fasi di lavoro, l’efficienza energetica è alta e si ha la possibilità di ridurre in modo consistente i consumi di combustibile.
Gli impianti di cogenerazione nella maggior parte dei casi sono costruiti direttamente nello stabilimento industriale, ottimizzando al massimo gli spazi disponibili in stabilimento costruendo un impianto su misura. L’investimento effettuato per l’installazione viene ripagato sul medio-breve periodo dal risparmio effettivo ottenuto. Inoltre, qualora si volesse procedere all’ installazione di un impianto di cogenerazione, in Italia si può approfittare dei vari incentivi destinati all’ efficientamento energetico, a patto che gli impianti vengano realizzati secondo i criteri della CAR (Cogenerazione ad Alto Rendimento), beneficiando dei certificati bianchi (TEE – Titoli di Efficientamento Energetico)
Conclusioni
L’analisi dei dati e delle informazioni fornite dai tecnici di uno stabilimento tessile consente spesso di mettere in luce aree di ottimizzazione. Ma questo risultato può essere validamente conseguibile soltanto a seguito di una Diagnosi energetica eseguita attraverso metodologie rigorose e dettagliate. A tal fine in Italia è di grande aiuto quanto messo a disposizione da Enea come ente anche di controllo delle Diagnosi energetiche, qualora obbligatorie per legge.
Sussistono comunque ampi spazi per migliorare anche gli aspetti gestionali, sia degli impianti produttivi (macchinari direttamente impiegati nella produzione), che degli ausiliari alla produzione stessa (distribuzione del vapore e produzione dell’aria compressa), oltre che interventi di carattere più orizzontale come la generazione di alcuni dei vettori energetici principali attraverso la cogenerazione e il fotovoltaico.
Didascalie
Figura 1
Schema tipico di impianto aria compressa. L’impianto di generazione dell’aria compressa è di solito una tra le aree più promettenti per attuare interventi di risparmio energetico.
Figura 2
Indici prestazione energetica. Nel caso specifico l’unita di prodotto può essere il metro di tessuto prodotto in uscita dallo stabilimento, costituendo in tal caso un indice generale che va riferito sia al consumo di energia elettrica.
Figura 3
Indici prestazione energetica relativi al consumo di gas naturale.
Figura 4
Opportunità di risparmio ottenibili attraverso l’adozione di interventi volti alla riduzione dei consumi oppure alla produzione efficiente di energia.
Figura 5
Impianto di cogenerazione ad uso industriale.