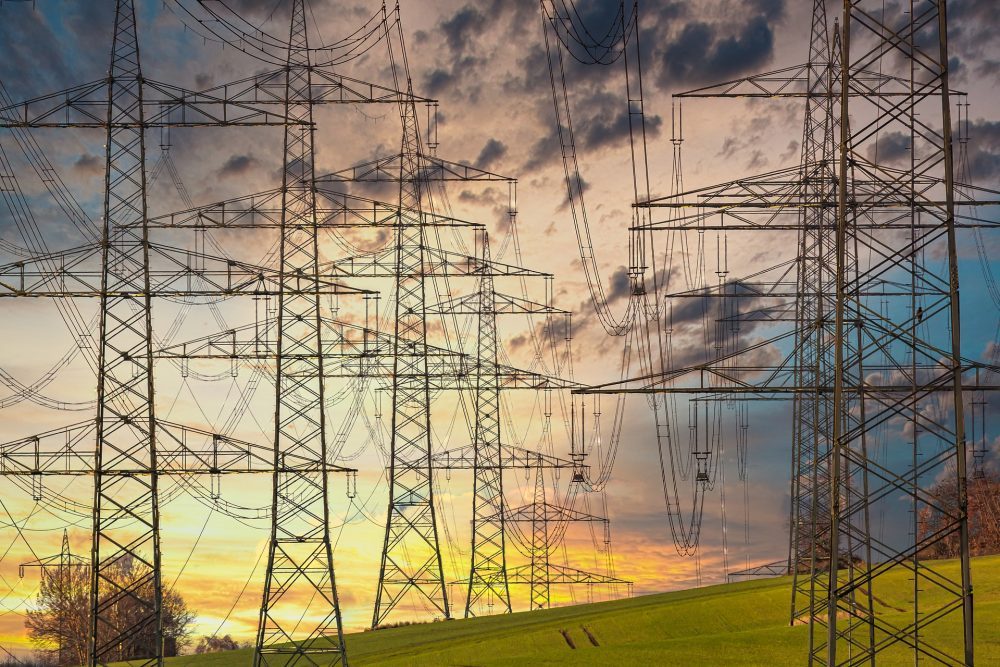
Risparmio energetico dalle macchine industriali
Progettare e costruire macchine efficienti riduce i consumi ma anche gli oneri di manutenzione, valorizza inoltre gli impianti di produzione dell’industria allungandone la vita utile.
Mai come ora il settore industriale è in prima linea sulle problematiche energetiche, di cui temiamo le conseguenze negative in modo particolarmente pressante. Parlando di efficienza energetica e di riduzione in generale dei costi, è possibile immaginare quale sia l’impatto sul cliente finale, attento oltreché agli aspetti economici, sempre più anche a quelli ambientali.
Gli operatori dell’industria sono consapevoli delle nuove sfide e hanno talvolta già sviluppato strategie finalizzate alla drastica riduzione dell’uso dell’energia nella produzione con riflessi sulla sostenibilità aziendale. E ciò ha un forte impatto sui costruttori delle macchine di produzione.
In materia di progettazione, in particolare, i costruttori sono impegnati nella realizzazione di nuove macchine che si adattino a questo nuovo e complesso mercato. Le soluzioni di automazione, ad esempio, hanno già dimostrato la loro efficienza e i loro vantaggi nella riduzione dell’uso dell’energia e del consumo di risorse nella produzione: in tal modo, gli utilizzatori aggiungono valore alle loro apparecchiature e si avvantaggiano rispetto alla concorrenza. Ma per rendere effettivi questi obiettivi, è al livello della progettazione che è possibile implementare tutti i benefici di una strategia mirata all’efficienza energetica. Di seguito si analizzano i punti salienti atti al raggiungimento degli obiettivi di efficienza energetica dei clienti aziendali e alla realizzazione di macchine o apparecchiature migliori in base alle relative applicazioni. Con la progettazione di macchine più efficienti dal punto di vista energetico, è possibile infatti risparmiare sui costi nell’intero ciclo di vita dell’apparecchiatura e tale riduzione dei costi può riflettersi direttamente sull’utente finale, l’impresa nel nostro caso, aumentando la competitività dell’azienda.
Sono già disponibili tecnologie frutto di una avanzata progettazione delle macchine, ed è possibile identificarne i temi principali, particolarmente dedicati agli aspetti elettrici di esse:
- scelta di motori elettrici correttamente dimensionati;
- utilizzo di motori elettrici ad alta efficienza;
- scelta di variatori di velocità adeguati;
- scelta di contattori e dispositivi di protezione appropriati;
- creazione di soluzioni più efficienti per il controllo movimenti;
- miglioramento dell’efficienza termica degli involucri;
- scelta delle tecnologie, degli strumenti e dei dispositivi di automazione (interfacce uomo macchina HMI – Human-Machine Interface, dimensionamento dei controllori ed altro)
- sviluppo della corretta architettura di automazione, ovvero l’impostazione delle logiche e della “filosofia” che sta alla base delle successive scelte relative alla componentistica.
I motori elettrici
L’importanza dei motori elettrici in ogni tipo di industria è evidenziata dai numeri: il 60% (valore ovviamente indicativo) dei consumi nei settori dell’industria e delle infrastrutture è dovuto ai motori elettrici.
In diversi settori industriali, ad esempio, pur essendo significativa la quota di investimenti sul processo (conta infatti più di un terzo degli investimenti totali), i consumi energetici correlati si dividono quasi equamente tra processo e altri servizi. Ciò significa che il lavoro di efficientamento sui motori elettrici, che sono i principali assorbitori di energia elettrica dei servizi ausiliari, può incidere molto sul bilancio complessivo di una unità produttiva. Importante però è conoscere “quanto” lavorano in termini di carico e di ore di funzionamento (Figura 1).
In generale, inoltre, gli attuatori delle macchine (motori elettrici, attuatori pneumatici ecc.) troppo spesso sono sovradimensionati, innalzando inutilmente i consumi delle macchine che, invece, una attenta progettazione potrebbe facilmente ridurre. Per di più, al fine di valutare il livello di solidità e affidabilità di una macchina è opportuno esaminare attentamente le applicazioni e le future evoluzioni che potrebbero rendersi necessarie; i motori più piccoli e più semplici sono comunque, in generale, da preferirsi. La correttezza del dimensionamento può in effetti ridurre il costo stesso delle macchine, oltre, come detto, quello di gestione operativa (Figura 2).
Dal punto di vista energetico, l’esperienza dimostra che l’uso di un motore dimensionato correttamente per l’applicazione che deve svolgere ottimizza i consumi energetici rispetto a un motore più potente. Questa considerazione fondamentale può garantire un risparmio del 3-4%, riducendo al tempo stesso i requisiti dimensionali del sistema di controllo dell’energia (ovvero il dimensionamento degli inverter).
L’introduzione di nuove norme, in particolare a partire dal 2015, in materia di motori ad alta efficienza, ha consentito di ottenere risultati aggiuntivi incoraggianti, a fronte di un costo che generalmente si ripaga in appena 1-2 anni. Il vantaggio supplementare della maggiore durata di un motore ad elevata efficienza contribuisce alla sostenibilità (ritardata sostituzione) e consente di preventivare un risparmio energetico di circa il 10%.
Variatori di velocità
Molteplici in ambito industriale sono le applicazioni che esigono carichi variabili (pompaggio, ventilazione e compressione di aria) e proprio per la gestione di questi servizi i variatori di velocità possono garantire vantaggi immediati e un risparmio energetico davvero consistente (fino al 50%).
Al tempo stesso, per qualunque applicazione che richieda l’avvio ripetitivo di macchinari (servizio intermittente), la scelta dei variatori di velocità rispetto ai tradizionali contattori consente di limitare la corrente di avviamento e di ridurre le perdite e i picchi di carico. I vantaggi istantanei per gli utenti finali (ad esempio il risparmio sulle bollette elettriche delle aziende) sono confortati da un ritorno degli investimenti inferiore a due anni.
Alcune applicazioni (ad esempio il sollevamento) possono sfruttare dispositivi che recuperano energia con l’impiego di unità rigenerative.
Architettura di automazione
Anche il sistema di controllo dell’automazione consuma energia (in sé stessa e non a livello di attuatori), ma è possibile ottimizzare tali consumi scegliendo le soluzioni più idonee. In funzione dell’applicazione, infatti, un’architettura di automazione più aderente alle effettive necessità può ridurre i consumi energetici del sistema di controllo globale. Un’architettura centralizzata, ad esempio, può persino dimezzare i consumi rispetto a un’architettura decentralizzata. Ma ciò non deve distogliere dal fatto che, a seconda della dimensione dell’applicazione, dei criteri di sicurezza e di rendimento, a volte sia necessario scegliere un’architettura decentralizzata; a questo punto però si può agire sul numero di fonti di alimentazione, il che può contribuire al risparmio energetico e a ridurre le perdite.
Le soluzioni di automazione più avanzate integrano controllori, sistemi di monitoraggio, interfacce uomo macchina HMI e reti in un sistema globale che fornisce un quadro completo dell’uso dell’energia. Grazie alle architetture di automazione “intelligenti” basate su standard aperti, i processi possono essere adattati alle effettive esigenze permanendo per lungo tempo sostenibili, a beneficio della produttività.
Misurazione e monitoraggio
Per incrementare l’efficienza energetica nell’industria, i consumi devono essere misurati anche a livello locale, in tempo reale, a partire dai dispositivi e dalle macchine (Figura 3).
La diffusione dell’automazione intelligente delle macchine e degli impianti produttivi può garantire maggiore efficienza, nei reparti produttivi come anche negli uffici.
Il livello di monitoraggio delle macchine consente la manutenzione preventiva per evitare guasti dei componenti, interruzioni della produzione e danni alle macchine o ai componenti, ma anche un’adeguata pianificazione, allo scopo di ridurre al minimo l’impatto sulla produzione e incrementare le opportunità commerciali per l’offerta di servizi a valore aggiunto (Figura 4).
L’esperienza dimostra che una strategia attiva per incrementare l’efficienza energetica consente di risparmiare, oltre alla materia energia, un ulteriore 8% (valore indicativo) grazie al rilevamento anticipato di eventuali discrepanze nei processi o nel ciclo di vita delle macchine. Gli operatori, il personale addetto alla manutenzione e i team di gestione della produzione possono così reagire rapidamente per porre rimedio alle condizioni che riducono l’efficienza delle macchine.
Conclusioni
Le aziende che sono state attente ai consumi energetici e hanno implementato sistemi di efficientamento dell’energia hanno effettivamente migliorato la produttività, ma anche l’impegno dei dipendenti e la competitività complessiva, ma molto resta da fare.
L’innovazione progettuale dei macchinari utilizzati e l’integrazione delle nuove tecnologie si ripercuotono sul costo finale di una macchina in una misura contenuta e stimata essere inferiore al 10%, a seconda dell’applicazione, ma i benefici vanno ben oltre quelli ipotizzabili.
E comunque, il risparmio energetico è un fattore decisionale imprescindibile per gli utenti industriali e rappresenta per chi opera nella produzione e nella manutenzione degli impianti una nuova opportunità, anche per distinguersi dalla concorrenza, apportando anche nuovi benefici come l’abbattimento degli sprechi, l’incremento della qualità ed il rendimento economico, con un ritorno degli investimenti spesso inferiore a due anni.
Didascalie
Figura 1
L’efficientamento sui motori elettrici prevede la conoscenza della distribuzione delle ore di funzionamento con la percentuale di carico in cui lavora il motore, come in questo grafico. (Blue Angel)
Figura 2
Costo globale (fatto 100) riscontrato durante il ciclo di vita di un motore elettrico (durata media di 15 anni) (Schneider Electric Industries)
Figura 3
Sistema di monitoraggio. Il livello di monitoraggio delle macchine consente la manutenzione preventiva per evitare guasti dei componenti, interruzioni della produzione e danni alle macchine o ai componenti.
Figura 4
Il contenimento dei consumi energetici si protrae nel tempo grazie al monitoraggio e controllo durante il ciclo di vita delle macchine. (Schneider Electric Industries)